Optimaliseren !?
Groeiende klachten van klanten
Stagnerende groei
Toenemende kosten
Veranderende marktomstandigheden
Overbelasting van medewerkers
…
Herken je één of meerdere van bovenstaande situaties, dan wordt het tijd om te gaan optimaliseren!
Wat is optimaliseren?
In de logistiek verstaan we onder optimaliseren;
“Het verbeteren van een proces met als doel de efficiency te verhogen, de kosten te verlagen en of de klantwaarde te verhogen”.
Dit klinkt eigenlijk allemaal vanzelfsprekend en toch is doelgericht optimaliseren in de praktijk lastiger dan dat het lijkt.
Uit het verleden is gebleken dat het juist optimaliseren van processen echt het verschil kan maken. Belangrijke voorbeelden van succesvolle optimalisaties uit de afgelopen jaren zijn onder andere gerealiseerd door “Henri Ford”, “Motorola” en “Toyota”. Door bewust en doelgericht te optimaliseren/ continu processen te verbeteren hebben deze bedrijven miljarden weten te besparen een enorme groei kunnen realiseren.
Onderstaand filmpje geeft een mooi beeld over de geschiedenis van optimaliseren.
Warehouse optimalisatie met Lean
Zoals in het filmpje is getoond is Lean ontstaan in de jaren '50 bij Toyota Motor Corporation in Japan, onder leiding van Taiichi Ohno en Eiji Toyoda. Het begon als een manier om productieprocessen te verbeteren en verspillingen te elimineren om zo meer waarde te creëren voor de klant. Het systeem werd later bekend als het Toyota Productie Systeem (TPS) en vormde de basis van de Lean-filosofie.
Het TPS werd ontwikkeld als reactie op de economische uitdagingen waar Toyota in die tijd mee te maken had. Het bedrijf had weinig financiële middelen en had te maken met een krappe markt, waardoor het zich niet kon veroorloven om veel voorraad aan te houden of veel kapitaal te investeren in machines en apparatuur. In plaats daarvan werd het TPS ontworpen om de efficiëntie te maximaliseren door middel van het elimineren van verspillingen en het optimaliseren van het productieproces.
Het TPS was gebaseerd op vijf kernprincipes: waardestroom, flow, pull, perfectie en respect voor mensen. Deze principes werden later uitgebreid en aangepast door Lean-experts als Womack en Jones, die het idee naar de Verenigde Staten brachten en het verder ontwikkelden tot wat nu bekend staat als de Lean-filosofie. Sindsdien is Lean uitgegroeid tot een wereldwijd toegepaste filosofie in verschillende industrieën en sectoren.
Lean vertaald naar een optimalisatie stappenplan
Stel je wordt gevraagd om een Warehouse of een bepaald logistiek proces te optimaliseren dan zijn de volgende stappen handig om te volgen
1. Identificeer de waardestroom
In eerste instantie doe je door de huidige processen zo goed als mogelijk in kaart te brengen. Veel toegepaste manieren om in de logistiek de waardestroom te identificeren of in kaart te brengen zijn;
- SIPOC
- Swimlane
- Procesanalyse
- Value Stream Mapping (VSM)
- Spaghetti Diagram
Meer informatie over de verschillende modellen vind je hier
2. Creer Flow
De tweede stap is het creëren van flow in het proces en de waardestroom te optimaliseren. Dit betekent dat je alle stappen in het proces moet bekijken om te bepalen welke stappen waarde toevoegen en welke stappen verspillingen zijn. Het beste doe je dit door op de voorgaande vastgelegde huidige processen elke stap in het proces nader te analyseren en te beoordelen wat in de specifieke stap wat niet goed gaat en beter kan. Methoden die je hiervoor kunt gebruiken zijn:
- 5S
- Ishikawa
- 5xWhy+1xHow
Meer informatie over de verschillende modellen vind je hier
3. Zorg voor Pull
De derde stap is om het proces “Pull” te maken. Dit betekent dat je ervoor zorgt dat het proces getriggerd wordt door de vraag van de klant en niet door het aanbod. Het doel is om de voorraad te verminderen, de reactietijd te verkorten en de transportkosten zo laag mogelijk te houden. Methoden hiervoor zijn onder andere;
- KanBan
- JIT
- Continues Flow
- Heijunka
Meer informatie over de verschillende modellen vind je hier
4. Streef naar perfectie
De vierde stap is om te streven naar perfectie. Dit betekent dat je voortdurend blijft verbeteren en verspillingen blijft elimineren. Het doel is om de efficiëntie en effectiviteit van het proces te optimaliseren. Binnen Lean kennen we onder andere de volgende methodieken;
- Kaizen
- Poka Yoke
- Jidoka
- Andon
- Hoshin Kanri
Meer informatie over de verschillende modellen vind je hier
5. Betrek medewerkers
De vijfde stap is om medewerkers te betrekken bij het optimaliseren van het proces. Dit betekent dat je hen betrekt bij het identificeren van verspillingen en het verbeteren van het proces. Het doel is om hun kennis en ervaring te benutten en hen te motiveren om bij te dragen aan de verbetering van het proces. Manieren om medewerkers te betrekken en betrokken te houden zijn onder andere;
- Training
- Kaizen-evenementen
- Dagelijkse Stand-Up voorafgaand aan een shift
- Visuele middelen zoals borden en grafieken
- Regelmatig geven van aandacht en tonen van empathie
Door het volgen van deze stappen kun je magazijnprocessen optimaliseren volgens de lean methodiek. Het is belangrijk om te beseffen dat lean niet iets is wat je eenmalig doet, maar een continu verbeterproces is.
Een veelgebruikte methodiek om het project op te zetten en te communiceren is het onderstaande A3 plan. Het A3 plan is gebaseerd op de DMAIC methode. De letters DMAIC staan voor; Define, Measure, Analyze, Improve en Control.
A3-Plan of Project Charter
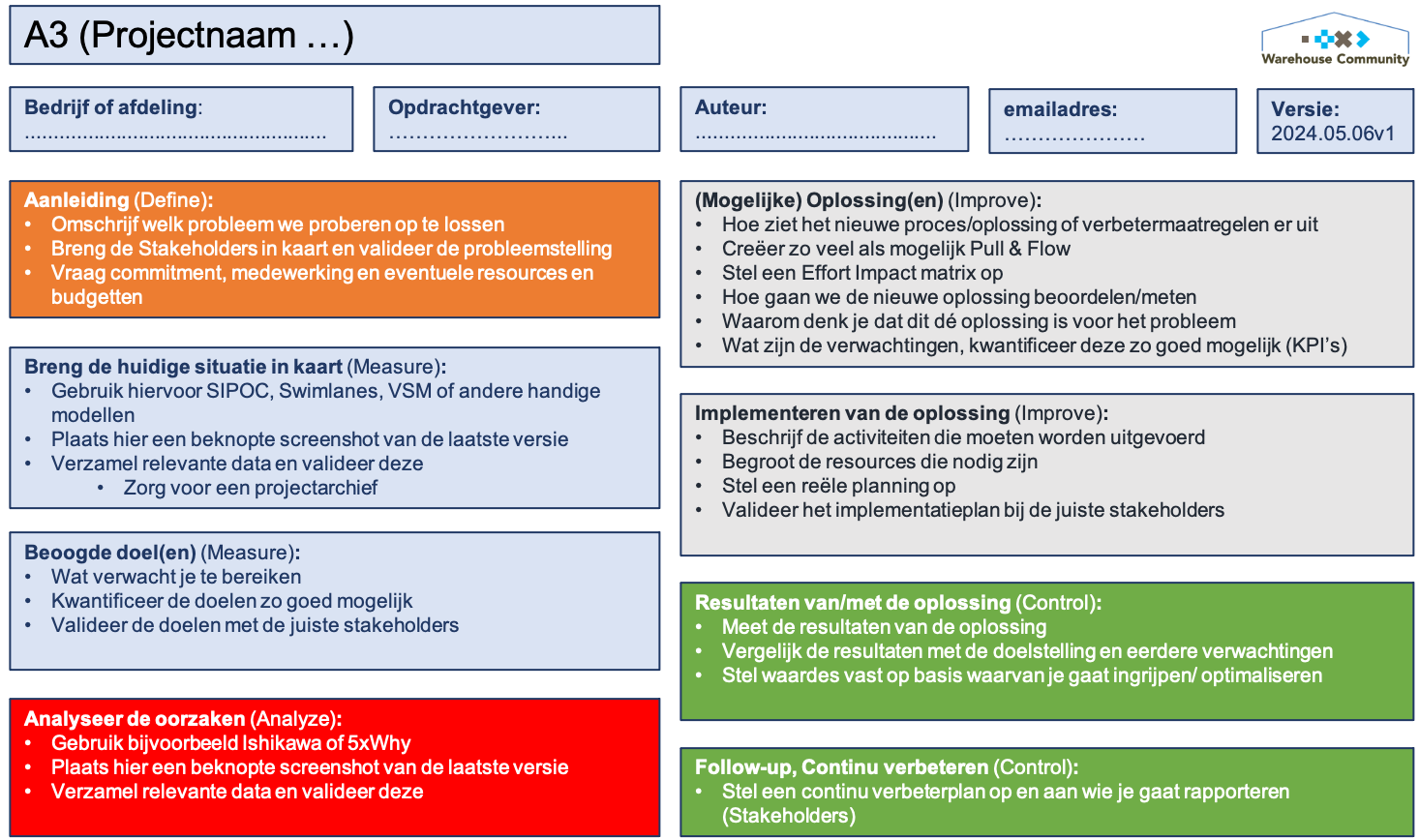
A3-plan of Project charter
Een A3-plan is een gestructureerde probleemoplossingmethode die wordt gebruikt binnen de Lean-filosofie. Het is vernoemd naar het A3-formaat papier waarop het plan wordt geschreven. Het A3-plan is bedoeld om problemen te analyseren en op te lossen, en om de communicatie en samenwerking binnen een team te verbeteren.
Het A3-plan is opgebouwd uit acht stappen welke een vertaling zijn vanuit de DMAIC methode. Elke stap wordt beschreven op een bepaald deel van het A3-formaat papier.
De stappen zijn:
1. Aanleiding (Define)
Dit onderdeel beschrijft het probleem en de context waarin het zich voordoet (Define).
Het uitwerken van een SIPOC of VSM (Values Stream Mapping) kan helpen bij het scherper in kaart brengen van het probleemgebied
2. Huidige situatie (Measure)
Verzamel gegevens over de huidige situatie en beschrijf de belangrijkste feiten en cijfers. (Measure)
Een grondige procesanalyse is noodzakelijk door bijvoorbeeld het uitwerken van een Swimlane of Spaghetti Diagram met bijbehorende procesdata.
3. Beoogde doelen (Measure)
Beschrijf het doel van het project en de gewenste uitkomst. (Measure eventueel via KPI's)
4. Oorzaak (Analyze)
Gebruik hierbij probleemoplossing technieken zoals de 5 Why's of Ishikawa-diagrammen om de oorzaak van het probleem te identificeren. (Analyze)
5. Oplossingen (Analyze)
Genereer en evalueer mogelijke oplossingen en kies de meest geschikte
Maak hier bijvoorbeeld gebruik van de Effort-Impact matrix
6. Implementatieplan (Improve)
Beschrijf het plan om de gekozen oplossing uit te voeren, inclusief tijdlijnen, verantwoordelijkheden en middelen. (Improve)
7. Resultaten (Control)
Meet de resultaten van de implementatie van de oplossing en vergelijk ze met de doelstellingen
8. Follow-up & Control
Bespreek hoe de oplossing in de toekomst kan worden verbeterd en geïmplementeerd op andere gebieden. (Control)
A3 als Communicatiemiddel
- Het A3-plan wordt vaak gebruikt in teams en kan dienen als een communicatiemiddel tussen verschillende afdelingen of functies binnen een organisatie. Het helpt bij het identificeren en oplossen van problemen en het verbeteren van de prestaties van een organisatie.
A3 Versiebeheer
- Een A3-plan kan nooit vanaf de 1e dag in zijn geheel worden ingevuld. Het project moet immers op stoom komen en de hoeveelheid aan informatie groeit met de tijd en de oplossing wordt uiteindelijk ook steeds concreter. Vandaar dat het raadzaam is om na elk belangrijk moment of vaststelling een nieuwe bijgewerkte versie van het A3-Plan uit te brengen. Belangrijk hierbij is de afspraak over het versiebeheer, oftewel wat is de laatste versie van het A3-plan en wie of hoe de versies en overige projectdocumenten worden beheert.
En nu?
Wie mag er starten met optimaliseren?
Welk magazijnproces wil jij optimaliseren?
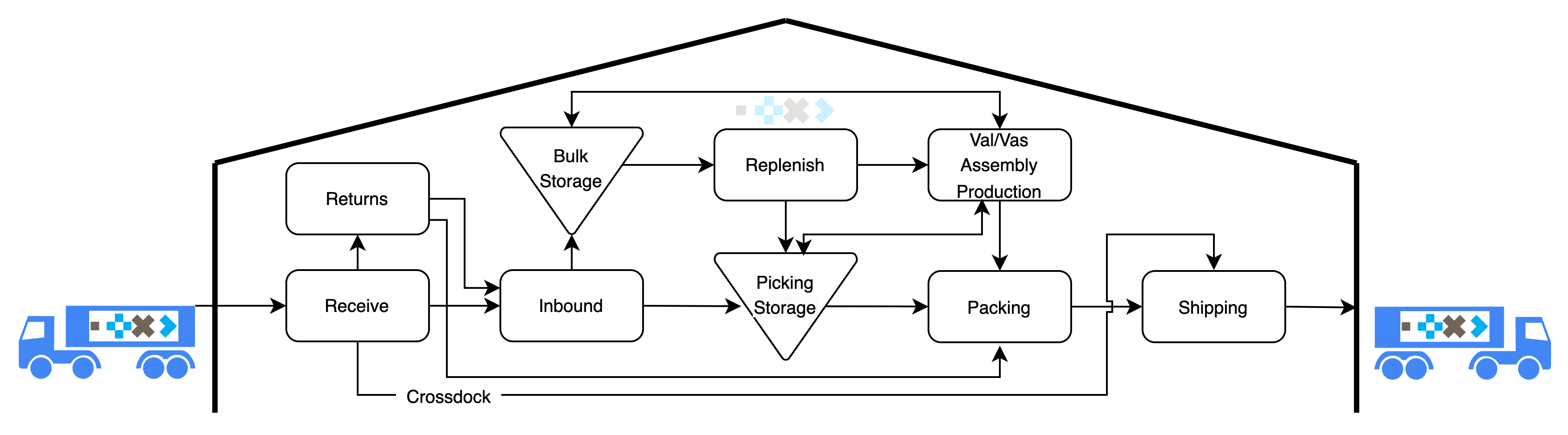
Optimaliseren door middel van logistieke challenges
Optimalisatie is een continue proces voor bedrijven die concurrerend willen blijven in een steeds veranderende markt. Een van de meest effectieve manieren om dit te doen is door middel van logistieke challenges. Deze challenges brengen studenten met verschillende achtergronden en kennis samen om op een creatieve manier oplossingen te bedenken voor problemen binnen uw bedrijf. Door de inzet van deze studenten worden nieuwe inzichten en ideeën aangedragen waar u als bedrijf niet eerder aan heeft gedacht. Door deze samenwerking wordt er tijd, geld en materiaal bespaard. Bovendien draagt u bij aan de ontwikkeling van toekomstige logistieke professionals.
Benieuwd naar de mogelijkheden?
- Klik hier door voor meer informatie over logistieke challenges.
- Klik hier door naar logistieke challenges binnen het logistiek onderwijs.
Deze pagina wordt regelmatig bijgewerkt
Ontvang automatisch de laatste updates gratis via LinkedIn
Of stel je vraag via info@warehouse-community.com